OM LESMO presents
improved techniques of processing strands with its
world renowned double twist technology ever sold:
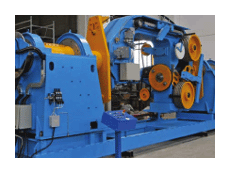
- Stranding of more than the usual 37 wires unilay
with the simultaneous stranding and compacting
of 61 aluminum and/or coppe rwires.
- Stranding of up to 37 member strands to a rope
of flexible copper up to 500 mm² in one pass
(battery and welding cables).
- The most interesting process and probably a
first ever, is the armouring of an insulated core
with mild steel wires on a double twist strander.
These processes were recently performed
on OM LESMO’S DTO-2500, a double
twist strander with the famous single bow system using
a 2500 mm (100”) diameter flange reel.
The continuous evolution of double-twist bunching
machines has made it possible for today's manufacturers
to strand and to Iay-up many types of products that
were un-imaginable on double-twist machines just a
few years ago. Products that have been traditionally
produced on rigid cage machines, tubular stranders
or single twist bunching machines are now easily manufactured
on today's broad family of double-twist bunching rnachines.
This has become substantial and undisputable and has
proved economic advantages of the new double-twist
technology.
NEW DOUBLE TWIST STRANDING MACHINE
“DTO2500”
O.M.Lesmo’s innovative
double twist technology has entered a new phase and
presents a new form of high speed double twist stranding
– the new DTO-2500 with a maximum reel diameter
of 2 500mm (100”)
This new machine is able to produce round highly-compacted
unilay conductors in copper (up to 280mm²) or
aluminium (up to 500 mm² = 1000MCM)) compacted
at top production speeds with maximum efficiency.
ADVANTAGES of
the DTO2500
- Possibility to produce from coils with a higher
wire capacity and therefore less changes and handling
time thereby increasing the efficiency of the
line . Also, in the case of spools with relevant
pay-offs, it is possible to save time in spools
change.
- Reduction of production cost
- Reduction in return on investment terms
- Reduction of power consumption
- External rotating capstan: double twist typical
bow stresses are not present
- Special Single carbon fiber bow delivers less
power consumption (less air resistance), less
heat and stress of the bearings, less noise level
and less maintenance time.
4/5 times higher speed than conventional machines
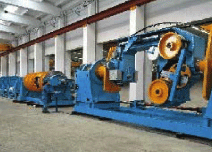
- Aerial strands ASCR with central wire in steel
and 6 wires in Aluminum
- Strands in Copper or Aluminum with 19 wires
(1+6+12) with 2 layers of wires stranded in contrary
lay and up to 61 wires unilay (1 + 6 +12 + 18
+ 24)
- Laying up of insulated cores rigid or flexible
|